El ferro és un element familiar per a totes les persones del nostre planeta. I no hi ha res d'estranyar en això. De fet, pel que fa al seu contingut a l'escorça terrestre (fins a un 5%), aquest component és el més comú. Tanmateix, només una quarantena part d'aquestes reserves es poden trobar en jaciments aptes per al desenvolupament. Els principals minerals del ferro són la siderita, el mineral de ferro marró, l'hematita i la magnetita.
Origen del nom
Per què el ferro té aquest nom? Si considerem la taula d'elements químics, aquest component està marcat com a "ferrum". S'abreuja com a Fe.
Segons molts etimòlegs, la paraula "ferro" ens va venir de la llengua protoeslau, en la qual sonava a zelezo. I aquest nom prové del lèxic dels antics grecs. Van anomenar el metall tan famós actual "ferro".
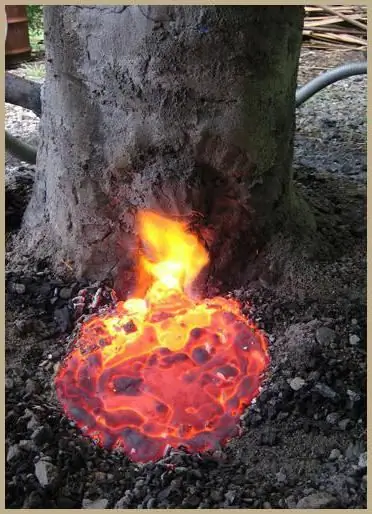
Hi ha una altra versió. Segons ella, el nom "ferro" ens va venir del llatí, onvolia dir "estrellat". L'explicació d'això rau en el fet que les primeres mostres d'aquest element descobertes per persones eren d'origen meteorit.
Ús de ferro
A la història de la humanitat, hi va haver un període en què la gent valorava més el ferro que l'or. Aquest fet queda recollit a l'Odissea d'Homer, que diu que als guanyadors dels jocs organitzats per Aquil·les se'ls va donar, a més d'or, una peça de ferro. Aquest metall era essencial per a gairebé tots els artesans, pagesos i guerrers. I va ser l'enorme necessitat d'ell el que es va convertir en el millor motor per a la producció d'aquest material, així com un major progrés tècnic en la seva fabricació.
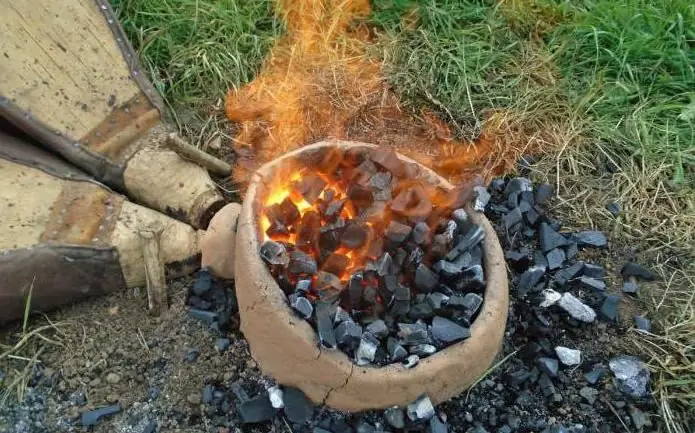
9-7 cc. BC. considerada l'edat del ferro en la història de la humanitat. Durant aquest període, moltes tribus i pobles d'Àsia i Europa van començar a desenvolupar la metal·lúrgia. No obstant això, el ferro encara té una gran demanda avui dia. Després de tot, segueix sent el principal material utilitzat per a la fabricació d'eines.
Producte de formatge
Quina és la tecnologia per produir ferro de floració, que la humanitat va començar a extreure als albors del desenvolupament de la metal·lúrgia? El primer mètode inventat per la humanitat es va anomenar fabricació de formatge. A més, va ser utilitzat durant 3000 anys, sense variar des del final de l'Edat del Bronze fins al període fins al segle XIII. L' alt forn no es va inventar a Europa. Aquest mètode es deia cru. Les banyes per a ell eren construïdes amb pedra o fang. De vegades, trossos d'escòria actuaven com a material per a les seves parets. L'última versió de la farga des de dins va serrecobert amb argila refractària, a la qual es va afegir sorra o banya triturada per millorar la qualitat.
Què fa que el ferro de flaix? Les fosses preparades s'omplien de mineral de prat o pantà "cru". L'espai de fusió d'aquests forns s'omplia de carbó vegetal, que després s'escalfava a fons. Al fons de la fossa hi havia un forat per al subministrament d'aire. Al principi, es va bufar amb manxes manuals, que després van ser substituïdes per mecàniques.
A les primeres fargues es va organitzar el tir natural. Es va dur a terme a través de forats especials - broquets, que es trobaven a les parets de la part inferior del forn. Sovint, els antics metal·lúrgics proporcionaven subministrament d'aire mitjançant l'ús d'un disseny que permetia obtenir l'efecte d'una canonada. Van crear un espai interior alt i alhora estret. Molt sovint, aquests forns es construïen al peu dels turons. Aquests llocs tenien la pressió del vent natural més gran, que s'utilitzava per augmentar la tracció.
Com a resultat del procés en curs, el mineral es va convertir en metall. Al mateix temps, la roca buida va baixar a poc a poc. Grans de ferro formats al fons del forn. Es van enganxar entre ells, convertint-se en l'anomenat "creep". Es tracta d'una massa esponjosa solta impregnada d'escòries. Al forn, la galeta estava blanca. Va ser en aquest estat que el van treure i ràpidament el van forjar. S'acaben de caure trossos d'escòria. A continuació, el material resultant es va soldar en una peça monolítica. El resultat va ser un ferro cridaner. El producte final tenia la forma d'un pa pla.
Què eracomposició del ferro de flor? Era un aliatge de Fe i carboni, que era molt petit en el producte final (si tenim en compte el percentatge, llavors no més de centèsimes).
No obstant això, el ferro florit que la gent rebia al forn cru no era molt dur i durador. És per això que els productes fets amb aquest material van fallar ràpidament. Les llances, les destrals i els ganivets estaven doblegats i no es van mantenir afilats durant molt de temps.
Acer
En la producció de ferro a les fargues, juntament amb els seus grumolls tous, també n'hi havia que tenien una duresa més elevada. Es tractava de peces de mineral que estaven en estret contacte amb el carbó vegetal durant el procés de fosa. Un home es va adonar d'aquest patró i va començar a augmentar deliberadament l'àrea en contacte amb el carbó. Això va permetre carburar el ferro. El metall resultant va començar a satisfer les necessitats dels artesans i els que utilitzaven productes fets amb ell.
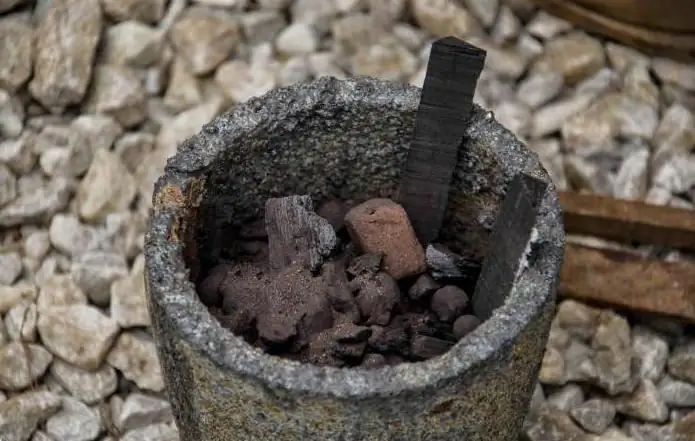
Aquest material era acer. Encara s'utilitza fins als nostres dies en la fabricació d'un gran nombre d'estructures i productes. L'acer, fos pels antics metal·lúrgics, és ferro flash, que conté fins a un 2% de carboni.
També hi havia una cosa com l'acer dolç. Era un ferro flash, que contenia menys del 0,25% de carboni. Si tenim en compte la història de la metal·lúrgia, llavors va ser l'acer suau el que es va produir en la fase inicial de la producció de formatge. Quin és un altre nom per al ferro de flaix? També hi ha una tercera varietat. Quan conté més d'un 2% de carboni, llavorsés de ferro colat.
Invenció de l' alt forn
El mètode de floració per obtenir ferro mitjançant forges de sang crua depenia molt del clima. Després de tot, per a aquesta tecnologia era important que el vent bufés al tub fabricat. Va ser el desig d'allunyar-se dels capricis del temps el que va portar a una persona a crear pells. Aquests eren els dispositius necessaris per ventilar el foc al forn de cru.
Després de l'aparició de la manxa, les fargues per a la producció de metall ja no es van construir als vessants. La gent va començar a utilitzar un nou tipus d'estufes, anomenades "foses de llops". Eren estructures, una part de les quals estava a terra, i la segona (les cases) s'alçava per sobre d'ella en forma d'estructura feta amb pedres unides per argila. A la base d'aquest forn hi havia un forat en el qual s'introduïa un tub de manxes per avivar el foc. El carbó que hi havia a la casa es va cremar, després de la qual cosa es va poder aconseguir el cracker. Es va treure pel forat, que es va formar després de l'eliminació de diverses pedres de la part inferior de l'estructura. A continuació, es va restaurar la paret i es va omplir el forn de mineral i carbó per començar de nou.

La producció de ferro brillant s'ha millorat constantment. Amb el temps, les cases van començar a construir-se més grans. Això va requerir un augment de la productivitat dels mecs. Com a resultat, el carbó va començar a cremar més ràpid, saturant el ferro amb carboni.
Ferro colat
Com es diu el ferro de flaix d' alt carboni? Tal com va seresmentat anteriorment, es tracta de ferro colat que és tan comú avui dia. La seva característica distintiva és la capacitat de fondre's a temperatures relativament baixes.
Ferro de maó - ferro colat en forma sòlida - era impossible de forjar. És per això que els antics metal·lúrgics no li van fer cas al principi. D'un sol cop amb un martell, aquest material simplement es va trencar en trossos. En aquest sentit, el ferro colat, així com l'escòria, es va considerar inicialment un producte de rebuig. A Anglaterra, aquest metall fins i tot s'anomenava "ferro brut". I només amb el temps, la gent es va adonar que aquest producte, encara que està en forma líquida, es pot abocar en motlles per obtenir diversos productes, per exemple, bales de canó. Gràcies a aquest descobriment als segles XIV-XV. a la indústria es va començar a construir alts forns per a la producció de ferro brut. L'alçada d'aquestes estructures va arribar als 3 metres o més. Amb la seva ajuda, es va fondre ferro de foneria per a la producció no només de bales de canó, sinó també dels mateixos canons.
Desenvolupament de la producció d' alts forns
Una autèntica revolució en el negoci metal·lúrgic es va produir als anys 80 del segle XVIII. Va ser llavors quan un dels empleats de Demidov va decidir que per a una major eficiència en el funcionament dels alts forns, l'aire s'havia de subministrar no a través d'un, sinó a través de dos broquets, que s'havien d'ubicar a banda i banda de la llar. A poc a poc, el nombre d'aquests broquets va créixer. Això va permetre fer més uniforme el procés de bufat, augmentar el diàmetre de la llar i augmentar la productivitat dels forns.
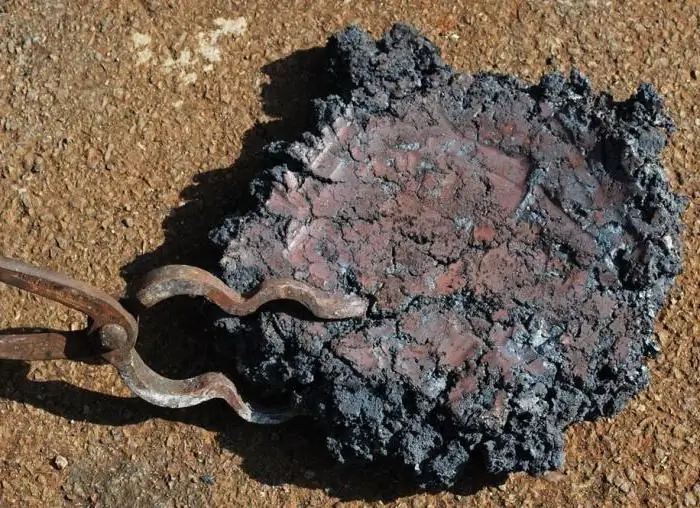
El desenvolupament de la producció d' alts forns també es va facilitar amb la substitució del carbó vegetal,per al qual es talaven boscos, per coca-cola. L'any 1829, a Escòcia, a la planta de Clayde, es va bufar aire calent a l' alt forn per primera vegada. Aquesta innovació va augmentar significativament la productivitat del forn i va reduir el consum de combustible. Actualment, el procés dels alts forns s'ha millorat substituint part del coc per gas natural, que té un cost encara més baix.
Bulat
Com es diu el ferro de flaix, que té propietats úniques que s'utilitzaven en la fabricació d'armes? Coneixem aquest material com acer damasc. Aquest metall, com l'acer de Damasc, és un aliatge de ferro i carboni. Tanmateix, a diferència de les seves altres espècies, és un ferro cridaner amb bones qualitats. És resistent i dur, i també és capaç de produir una afilada excepcional a la fulla.
Els metal·lúrgics de molts països porten més d'un segle intentant desvelar el secret de la producció d'acer damasc. Es van proposar un gran nombre de receptes i mètodes que incloïen l'addició d'ivori, pedres precioses, or i plata al ferro. No obstant això, el secret de l'acer damasc va ser revelat només a la primera meitat del segle XX pel notable metal·lúrgic rus P. P. Anosov. Van agafar ferro florit, que es posava en un forn amb carbó vegetal, on cremava un foc obert. El metall fos, saturat de carboni. En aquella època, estava cobert amb escòries de dolomita cristal·lina, de vegades amb l'addició de l'escala de ferro més pura. Sota aquesta capa, el metall es va alliberar molt intensament de silici, fòsfor, sofre i oxigen. Tanmateix, això no va ser tot. L'acer resultant s'havia de refredar el màxim possiblemés lent i tranquil. Això va permetre formar, en primer lloc, grans cristalls d'estructura ramificada (dendrites). Aquest refredament es va fer directament a la llar, que estava plena de carbó calent. A la següent etapa, es va dur a terme una forja hàbil, durant la qual l'estructura resultant no s'hauria de col·lapsar.
Les propietats úniques de l'acer damasc van trobar una explicació posterior als treballs d'un altre metal·lúrgic rus D. K. Chernov. Va explicar que les dendrites són acers refractaris però relativament tous. L'espai entre les seves "branques" en el procés de solidificació del ferro s'omple de carboni més saturat. És a dir, l'acer tou està envoltat d'acer més dur. Això explica les propietats de l'acer damasc, contingudes en la seva viscositat i alhora d' alta resistència. Aquest híbrid d'acer durant la fusió conserva la seva estructura d'arbre, convertint-lo només d'una línia recta a una en ziga-zaga. La peculiaritat del patró resultant depèn en gran mesura de la direcció dels cops, la força, així com l'habilitat del ferrer.
Acer de Damasc
A l'antiguitat, aquest metall era el mateix acer damasc. Tanmateix, una mica més tard, l'acer de Damasc va començar a anomenar-se un material obtingut per soldadura de forja a partir d'un gran nombre de filferros o tires. Aquests elements estaven fets d'acer. A més, cadascun d'ells es caracteritzava per un contingut de carboni diferent.
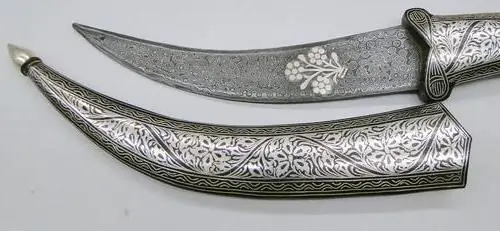
L'art de fabricar aquest metall va assolir el seu màxim desenvolupament a l'edat mitjana. Per exemple, en l'estructura de la coneguda fulla japonesa, van trobar els investigadorsuns 4 milions de fils d'acer de gruix microscòpic. Aquesta composició va fer que el procés de fabricació d'armes fos molt laboriós.
Producció en condicions modernes
Els metal·lúrgics antics van deixar una mostra de la seva habilitat no només en armes. L'exemple més cridaner de ferro florit pur és la famosa columna situada prop de la capital de l'Índia. Els arqueòlegs van determinar l'edat d'aquest monument d'art metal·lúrgic. Va resultar que la columna es va construir fa 1,5 mil anys més. Però el més sorprenent rau en el fet que avui dia és impossible detectar fins i tot petits rastres de corrosió a la seva superfície. El material de la columna va ser sotmès a un examen acurat. Va resultar que es tracta de ferro flash pur, que només conté un 0,28% d'impureses. Aquest descobriment va sorprendre fins i tot els metal·lúrgics moderns.
Amb el temps, el ferro cridaner va anar perdent la seva popularitat. El metall fos en una llar oberta o alt forn va començar a gaudir de la major demanda. Tanmateix, en aplicar aquests mètodes, s'obté un producte de puresa insuficient. És per això que el mètode més antic de producció d'aquest material ha rebut recentment la seva segona vida, que permet produir metalls amb les característiques de màxima qualitat.
Com es diu el ferro de flaix avui? Ens és familiar com a metall de reducció directa. Per descomptat, el ferro florit avui no es produeix de la mateixa manera que en l'antiguitat. Per a la seva producció s'utilitzen les tecnologies més modernes. Permeten produir metall que pràcticament no téimpureses estranyes. En la producció s'utilitzen forns de tubs rotatius. Aquests elements estructurals s'utilitzen per a la cocció de diversos materials a granel amb altes temperatures en la indústria química, del ciment i en moltes altres indústries.
Com es diu ara el ferro de flaix? Es considera pur i s'utilitza per obtenir un mètode que en essència no és gaire diferent del que existia en l'antiguitat. Tot i així, els metal·lúrgics utilitzen mineral de ferro, que s'escalfa en el procés d'obtenció del producte final. Tanmateix, avui dia les matèries primeres estan sotmeses inicialment a un processament addicional. S'enriqueix, creant una mena de concentrat.
La indústria moderna utilitza dos mètodes. Tots dos us permeten obtenir ferro de flaix del concentrat.
El primer d'aquests mètodes es basa a portar les matèries primeres a la temperatura requerida mitjançant combustible sòlid. Aquest procés és molt semblant al dut a terme pels antics metal·lúrgics. En lloc de combustible sòlid, es pot utilitzar gas, que és una combinació d'hidrogen i monòxid de carboni.
Què precedeix obtenir aquest material? Com es diu avui en dia el flash iron? Després d'escalfar el concentrat de mineral de ferro, els pellets romanen al forn. A partir d'ells es produeix posteriorment metall pur.
El segon mètode utilitzat per restaurar el ferro és molt similar en tecnologia al primer. L'única diferència és que els metal·lúrgics utilitzen hidrogen pur com a combustible per escalfar el concentrat. Amb aquest mètode, el ferro s'obté molt més ràpidament. Exactamentper tant, es distingeix per una qualitat superior, perquè en el procés d'interacció de l'hidrogen amb el mineral enriquit només s'obtenen dues substàncies. El primer d'ells és ferro pur, i el segon és aigua. Es podria suposar que aquest mètode és molt popular en la metal·lúrgia moderna. Tanmateix, avui s'utilitza amb poca freqüència i, per regla general, només per a la producció de pols de ferro. Això s'explica pel fet que és bastant difícil obtenir hidrogen pur, tant per resoldre problemes tècnics com per dificultats econòmiques. L'emmagatzematge del combustible rebut també és una tasca difícil.
Fa relativament poc temps, els científics han desenvolupat un altre tercer mètode per a la producció de ferro reduït. Es tracta d'obtenir metall a partir del concentrat de mineral, sense passar per l'etapa de la seva transformació en pellets. Els estudis han demostrat que amb aquest mètode es pot produir ferro pur molt més ràpidament. Tanmateix, aquest mètode encara no s'ha implantat a la indústria, ja que requereix canvis tecnològics importants i un canvi en l'equipament de les empreses metal·lúrgiques.
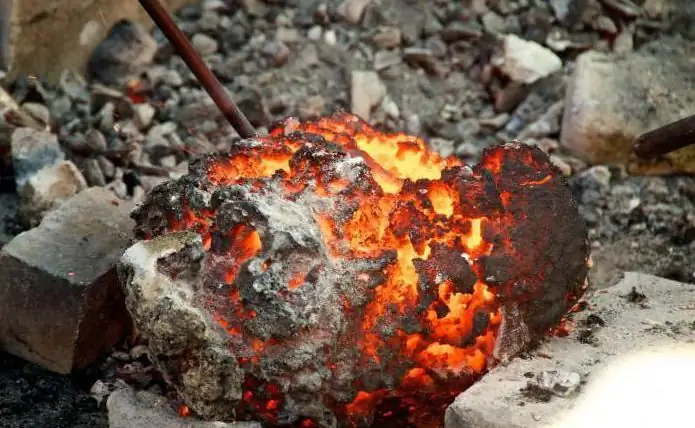
Com es diu avui el ferro de flaix? Aquest material ens és familiar com a metall de reducció directa, de vegades també s'anomena esponjós. Aquest és un material rendible, d' alta qualitat i respectuós amb el medi ambient que no conté impureses de fòsfor i sofre. Per les seves característiques, el ferro florit s'utilitza a les indústries d'enginyeria (aviació, construcció naval i instrumentació).
Fechral
Com podeu veure, avui quan feu servirles tecnologies més modernes utilitzen materials com el ferro florit. Fechral també és un aliatge molt buscat. A més del ferro, conté components com el crom i l'alumini. El níquel també està present a la seva estructura, però no més del 0,6%.
Fechral té una bona resistència elèctrica, una gran duresa, funciona molt bé amb ceràmiques d' alta alúmina, no té tendència a picar i és resistent a la calor en una atmosfera que conté sofre i els seus compostos, hidrogen i carboni. Però la presència de ferro a l'aliatge el fa bastant trencadís, cosa que dificulta el processament del material en la fabricació de diversos productes.
Fechral s'utilitza en la fabricació d'elements de calefacció per a forns de laboratori i industrials, la temperatura màxima de funcionament dels quals és de 1400 graus. De vegades, les peces d'aquest aliatge s'utilitzen per a altres finalitats. Es col·loquen en aparells de calefacció domèstics, així com en aparells elèctrics d'acció tèrmica. Fechral s'ha utilitzat àmpliament en la producció de cigarrets electrònics. A més, un aliatge de ferro, alumini i crom és demanat en el camp de la fabricació d'elements resistius. Aquestes poden ser, per exemple, resistències d'arrencada i frenada de locomotores elèctriques.
Fechral s'utilitza per produir filferro, així com fil i cinta. De vegades s'obtenen cercles i varetes. Tots aquests productes s'utilitzen en la fabricació de diferents tipus d'escalfadors per a forns elèctrics.